Dr. James Yang develops highly-accurate anthropometric digital human models
Edited by Javad Hashemi and Jeff Sammons
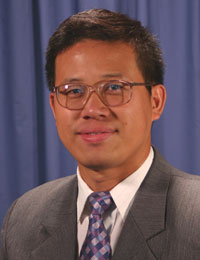
Dr. James Yang, an assistant professor of mechanical engineering and the director of the Human-Centric Design Research laboratory at Texas Tech, is developing computer-based human simulations that aid in the development of products, vehicles, safety devices, and procedures.
Any product or device that is designed to be used by people must take into account the variability of the human population for which the product is intended for. As an example, when designing for human variability in the interior cab of a vehicle, it becomes difficult to predict an optimum driver seat adjustment range that will suit any user. In another example, emergency workers, skilled laborers, and healthcare professionals use masks or respirators to work in potentially hazardous, harsh, or diverse environments. Respirator use is an integral part of occupational safety and health practice. Mask designers must create respirators with the best fit and highest comfort level for workers of various ages and face characteristics. Human-centric design addresses such issues in the development of products.
In the past, human-centric designs could only be tested on actual subjects or on prototypes. Identifying sample populations for testing or developing a broad range of prototypes was time consuming and costly. Even with the advent of human simulations on computers, the analysis was expensive and one test could take several weeks to complete.
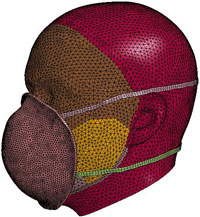
Yang has developed a new optimization-based approach to handle the simulation of humans and the simulation of the interactions between humans and various products and devices. His modeling is inexpensive, provides nearly real-time results, can provide more than 100 degrees of freedom in the human model.
Yang places anthropometric digital human models in a 3D test environment to perform various tests. His models are able to take skin, muscles, bones, joints, and other body elements into account as he analyzes ergonomics and comfort.
He has worked with the Department of Defense, NASA, the National Science Foundation, Honda R&D Americas Inc, Caterpillar, the National Institute for Occupational Safety and Health, National Institute of Standards and Technology, and other organizations to test respirators, helmets, goggles, seatbelts, firefighters, masks, respirators, pregnant women, joysticks, space environments, sporting activities, tank operators, and other items and situations.
Yang's model is different from other simulations because he incorporates physics into his models. Utilizing certain human performance measures, he is able to accurately predict forces, stresses, pain, comfort, injury, and contact points. His simulations can also help in determining why certain products fail and how certain harmful situations could potentially happen.
His simulations save time and money for manufacturers because they can test various materials in extreme situations without high expenses and long testing durations. For consumers, Yang's models provide companies with the opportunity to make optimally-designed products.
Yang worked with a car manufacturer to design a vehicle environment that is suited for a wide range of people. His simulation predicted the optimum posture of the seated driver inside the vehicle and gave an indication of how comfortable the driver is while seated in the predicted posture.
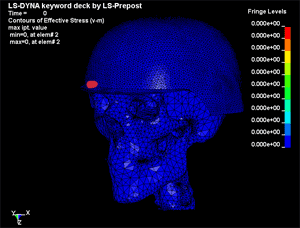
In military applications, he has incorporated ballistic helmets with his models. For soldiers, ballistic impact is one of the major causes for traumatic brain injury (TBI) and ballistic helmets are designed to provide protection from TBI. In real life, it is impossible to use real human subjects for experiments. Therefore, simulation based-methods are convenient to assess the rear effect to ballistic helmet impact and can provide crucial insights to injury. Rear effect happens when the interior of helmet is deformed and contacts with the human head. Yang tested the ballistic helmeted headform under impact from a bullet with different impact angles and at various impact positions. He used a high fidelity headform model including detailed skull and brain to determine that the bullet from behind a soldier poses the most danger.
In the future, he hopes to expand his models to include other body elements, including tendons, organs, glands, and more finite elements, like vessels and nerves. He also plans to develop predictive ride models that analyze the comfort of riding in an automobile, even at the prototype phase. His hope is to be able to continue to adjust and improve products and devices, in order to increase safety, and save time and money for consumers and manufacturers.
Yang joined the Department of Mechanical Engineering in the Whitacre College of Engineering as an assistant professor in 2008. Yang received a Bachelor of Science in Vehicle Engineering and a Master of Science in Automobile Engineering from Jilin University in China. He received a Doctor of Philosophy in Mechanical Engineering from The University of Iowa.
Yang has authored more than 170 journal and conference publications, and has written or contributed to eight book chapters.
Edward E. Whitacre Jr. College of Engineering
-
Address
100 Engineering Center Box 43103 Lubbock, Texas 79409-3103 -
Phone
806.742.3451 -
Email
webmaster.coe@ttu.edu